STRENGTHENING DEEPWATER DRILLSHIP OPERATIONS
Fortune 500 equipment provider gets turnkey support strengthening a critical riser component—and operator confidence.
Drillships deliver a mission-critical part of field operations; and often there’s no second chance to get it right. One major global equipment provider turned to PCC Energy Group to enhance the structural integrity of an essential drillship riser component, ensuring this strategic asset would be online when needed by the operator.
The Challenge
Hydraulic riser running tool components all work together to add, remove and run riser or specialty joints to the riser stack-and are vital to the operation of drillship installations worldwide. Riser pipe is the gateway to the well, so if one component fails the entire operation is put at risk. Fail-safes are in place, but any component that's lost also means a loss in customer confidence for both the contractor and operator-even if the project can technically continue.
So when a major provider of drillship equipment recognized riser system component galling as a repeated issue, they consulted with PCC Energy Group on how to develop more durable, corrosion-resistant hydraulic riser running tool components.
Application
High stress component in hydraulic riser running tool
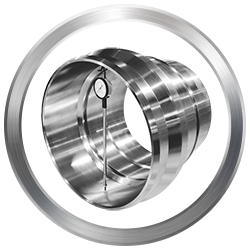
Benefits
- Mitigated galling
- Increased durability and longevity
- Provided superior corrosion resistance
Features
- Minimum Yield Strength of 160 ksi
- Adherence to stringent NACE MR0175/ISO-15156-3
- Age hardenable nickel-iron-chromium alloy with molybendum, copper, niobium, titanium and aluminum
The Solution
PCC Energy Group consulted with the upstream systems provider to determine the perfect alloy for the application, engineer the component, forge the alloy and machine the part to spec-bringing superior knowledge of materials and specialty processes at every step of the way. From specification to testing, PCC Energy Group performed everything in-house.
The company's metallurgists and engineers selected INCOLOY® alloy 945X®-which would mitigate the catastrophic system effects of galling caused by component friction and adhesion. Nobody understands how to work with an alloy better than the company that created it, so the components were engineered, forged and machined with 100 percent confidence of project success. In fact, approximately 80 percent of all high-performance PH Grade nickel alloys used upstream were invented by PCC Energy Group metallurgists.
Altogether, from concept to quality control, the company was able to deliver a finished component to the equipment provider in just three months.
The Benefits
The system’s new hydraulic riser running tool delivered superior structural integrity and more confidence to the operator and drilling contractor. It also enabled less operational risk and afforded a significant level of avoided opportunity cost. If the component galling had been left unchecked, the riser system could have failed. Depending on market conditions, drillship day rates can cost operators more than $500,000 per day. Using INCOLOY® alloy 945X® and leveraging the company’s materials expertise meant far greater structural integrity for the riser running tool—mitigating potential galling and reducing the prospect of downtime for required repairs and time out of service. Ultimately the equipment provider, drilling contractor and operator were able to strengthen their operations knowing the riser system would run smoothly even under intensive service.